محصولات شوینده سطوح عموما از ترکیبات اسیدی ساخته شده که بدلیل ارزان بودن مواد بسته بندی شده از اسیدهای خطرناک رقیق شده استفاده شده است مانند اسید سولفوریک
جوهر نمک (هیدروکلریک اسید) چیست؟
جوهر نمک (HCL) یا هیدروکلریک اسید که با نام های دیگری همچون اسیدم سالیس و نمک اسید نیز شناخته شده می باشد، از قوی ترین اسیدهای مورد استفاده در محیط های صنعتی و تصفیه آب و فاضلاب به شمار می رود. این ترکیب بسیار خورنده بوده و استشمام بوی تند آن منجر به مشکلات تنفسی و مسمویت می گردد. اسید کلریدریک تاثیر بسیار بالایی از نظر رسوب زدایی و جرم گیری داشته و در صنایع مختلف از جمله تولید فولاد و آبکاری و اسیدشویی فلزات مورد استفاده قرار میگیرد. گروه صنعتی هفت؛ ارائه دهنده مواد شیمیایی تصفیه آب و فاضلاب در ادامه به معرفی کامل هیدروکلریک اسید پرداخته و نحوه تولید، قیمت و موارد مهم در خرید و کاربردهای آن را شرح داده و به این سوال نیز پاسخ خواهد داد که جوهر نمک چه تفاوتی با وایتکس دارد؟
آنچه در این مطلب می خوانید:
جوهر نمک یا هیدروکلریک اسید چیست؟
اسید هیدروکلریک یا HCL که با نام های دیگری از قبیل تیرک و همچنین نمک اسید و اسید کلریدریک نیز شناخته شده می باشد، این ماده اسیدی بی رنگ بوده و قدرت خورندگی بسیار بالایی داشته و گزینه ای بسیار کاربردی برای جرم گیری به شمار می رود. علاوه بر تاثیراتی که بر حذف رسوبات از روی سطوح و تاسیسات مختلف دارد، از جوهر نمک برای تولید مواد پلاستیکی پی وی سی و همچنین مواد منعقد کننده نیز در صنایع مختلف استفاده میشود. بر اساس اسناد موجود، برای اولین بار هیدروکلریک اسید یا جوهر نمک در قرن 16 میلادی توسط آندریاس لیباویوس تهیه شده است که از حرارت دهی نمک در بوته چینی گل رس بدست آمده است.
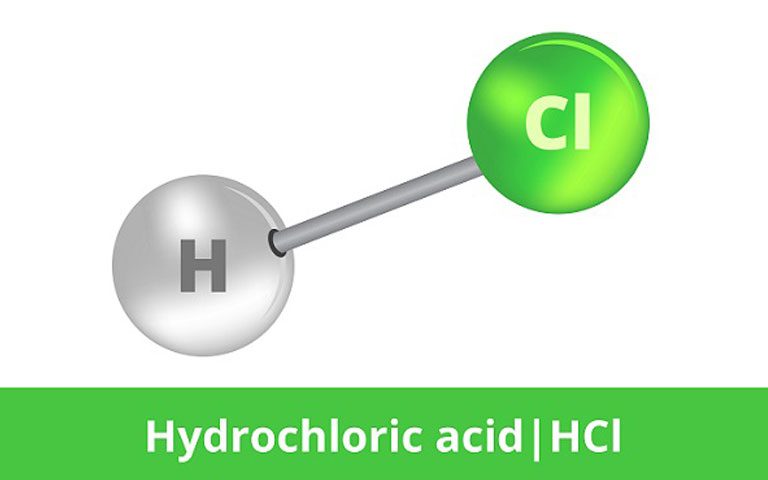
PH جوهر نمک چقدر است؟
طبق استانداردها PH جوهر نمک (هیدروکلریک اسید) بین 0 تا 2 می باشد. یعنی به نوعی میتوان گفت پی اچ جوهر نمک کمتر از 2 میباشد.
نحوه تولید و فرمول ساخت جوهر نمک
برای تهیه اسید کلریدریک یا جوهر نمک روش های متعددی وجود دارد که از جمله آنها می توان به استفاده از نمک طعام اشاره نمود. البته در روش های تولید هیدروکلریک اسید در صنعت از هیدروژن کلرید و آب استفاده میشود و در نهایت خروجی آن اسید با درجه خلوص 38 درصد می باشد. در صورتیکه از نمک معمولی و اسید سولفوریک برای تولید این اسید استفاده شود، واکنش های زیر را شاهد خواهیم بود:
NaCl + H2SO4 ——> HCl + NaHSO4
NaCl+H2NaHSO4———-> HCl + Na2SO4
در این روش لازم است علاوه بر نمک و اسید سولفوریک، از خمیر نیترات نیز استفاده شود و حرارت دهی انجام شود.
در روش دیگری که بیشتر معمول می باشد، از هیدروژن و کلر برای تهیه هیدروکلریک استفاده میشود که فرمول واکنش آن به صورت زیر است:
H2 + Cl2 ———–> ۲HCl
در این روش ابتدا کلر و هیدروژن را حرارت دهی می کنند تا کلر بسوزد و کلروهیدروژن تولید شود. بری حرارت دهی کلر و هیدروژن از کوره های سیلیکاتی استفاده میشود و در نهایت کلروهیدروژن سرد و جذب شده و اسید کلریدریک بدست خواهد آمد.
ویژگی های فیزیکی و شیمیایی جوهر نمک یا هیدروکلریک اسید
جوهر نمک یا فرمول شیمیایی HCL بی رنگ با بوی بسیار تند و زننده می باشد که قدرت خورندگی بسیار بالایی دارد و در تصفیه آب مورد استفاده قرار میگیرد. جرم مولکولی این ماده اسیدی 36.46 گرم بر مول بوده و خلوص آن در بازه 30 تا 37 درصد می باشد. لازم به ذکر است که اسید کلریدریک با خلوص بیش از 40 درصد بسیار فرار بوده و لازم است در محیط های دربسته با شرایط دمایی مناسب نگهداری شود. جوهر نمک در دمای -35 درجه سانتی گراد ذوب و در 108 درجه سانتی گراد به جوش میرسد و قابل اشتعال نمی باشد، اما براحتی در آب حل می گردد.
واکنش جوهر نمک با فلزات
همان طور که در طول متن اشاره شد، این ماده اسیدی بسیار خورنده بوده و در صنایع مختلف و تولید فلزات و آبکاری و فولاد مورد استفاده قرار میگیرد. آهن و قلع و فلزاتی که بر پایه این دو می باشند، در تماس با جوهر نمک حل میشوند. از این خاصیت برای حذف قلع و لحیم قطعات الکترونیکی به وفور استفاده میشود. لازم به ذکر است که اسید کلریدریک قادر به حل کردن فلزات گرانبها و همچنین مس نمی باشد.
تفاوت جوهر نمک و وایتکس چیست؟
یکی از اشتباهات رایج این است که اغلب افراد وایتکس و جوهر نمک را یکسان در نظر میگیرند. این دو ماده شیمیایی که هر دو دارای خاصیت تمیزکنندگی بالا می باشند، از نظر نوع ترکیبات موجود در آنها با هم متفاوت می باشند. وایتکس که در واقع همان سدیم هیپوکلریت می باشد، از سدیم و کلر تشکیل شده و به عنوان یک ماده قلیایی مورد استفاده قرار میگیرد. این در حالیست که هیدروکلریک اسید دارای PH کمتر از 2 بوده و یک اسید بسیار قوی با خاصیت خورندگی می باشد. به همین دلیل جوهر نمک لک های سیاه را بر روی سطوح فلزی و کاشی و سرمیک ایجاد می کند اما وایتکس چنین خاصیتی ندارد. توجه داشته باشید که ترکیب این دو ماده بسیار خطرناک می باشد.
تفاوت جرمگیر و جوهرنمک چیست؟
تفاوت جوهر نمک و جرمگیر تا حد زیادی به نوع مصرف و کاربرد آنها و همچنین قدرت اسیدی این دو محلول مرتبط می باشد. جوهر نمک یا هیدروکسید اسید ماده ای با قدرت اسیدی بسیار بالا در بزه 0 تا 20 می باشد که بیشتر در صنعت مورد استفاده قرار میکیرد. از این مواد برای از بین بردن رسوب های قوی و خالص سازی استفاده میشود. این در حالیست که جرم گیر ها قدرت اسیدی ضعیف تری داشته و بیشتر برای ایجاد جلا و از بین بردن لک های روشی کاشی و سرامیک مورد استفاده قرار میگیرند.
کاربرد جوهر نمک در تصفیه آب
کاربرد جوهر نمک در صنایع مختلف از جمله تولید فولاد و فلزات، صنایع غذایی و همچنین سفید کردن کاغذ و غیره مورد استفاده قرار میگیرد. از مهم ترین کاربردهای این مواد اسیدی می توان به تصفیه آب و فاضلاب اشاره نمود. هیدروکلریک اسید در فرآیند تولید آهن کلرید و پلی آلومینیوم کلرید که از مواد منعقد کننده قوی می باشند استفاده میشود. استفاده از این مواد برای حذف ذرات کلوئیدی و معلق در حوضچه های تصفیه فاضلاب و آب کاربرد زیادی دارد.
از دیگر موارد کاربرد اسید کلریدریک می توان به بازسازی رزین های کاتیونی مورد استفاده در تجهیزات تصفیه آب از قبیل سختی گیر ها اشاره نمود. توجه داشته باشید که عدم رعایت اصول ایمنی در زمان استفاده از این مواد اسیدی مشکلات متعددی از قبیل سوزش پوست، مسمومیت و مشکلات تنفسی و خفگی را به همراه خواهد داشت.

کاربرد هیدروکلریک اسید در استخرها
از جوهر نمک در تصفیه آب استخر و همچنین جرم گیری کاشی و سرامیک کف و دیواره های آن مورد استفاده قرار میگیرد. این مواد به دلیل خورندگی بسیار بالا باید به مقدار بسیار کم و به نسبت 1 به 100 لیتر آب استفاده شود در غیر این صورت منجر به سیاه و لک شدن و از بین رفتن لعاب روی کاشی و سرامیک خواهد شد.
همچنین لازم به ذکر است که پس از استفاده از کلر مایع یا پودر کلر در استخرها، مقدار PH ممکن است با تغییراتی مواجه شود که عدم کنترل آن می تواند منجر به بیماری های پوستی گردد. درشرایطی که خاصیت قلیاییت آب پس از کلر زنی افزایش پیدا میکند، با تزریق مقدار کمی از جوهر نمک می توان مقدار PH را در سطح استاندارد تنظیم نمود.
خرید جوهر نمک
درجه خلوص اسید کلریدریک اهمیت بسیار زیادی داشته و با توجه به نوع کاربرد آن از گزینه های مختلفی برای این منظور استفاده میشود. به عنوان مثال، خرید جوهر نمک مورد استفاده برای محیط های صنعتی می تواند درجه خلوص بالا و حدود 37 درصد داشته و برای مصارف خانگی حدود 10 تا 12 درصد مورد استفاده قرار میگیرد.
____________________________________
لاستیک SBR چیست؟
لاستیک SBR، یا لاستیک استایرن-بوتادین، یک لاستیک مصنوعی است که از کوپلیمریزاسیون استایرن و بوتادین به دست میآید. این لاستیک ابتدا به عنوان جایگزینی برای لاستیک طبیعی در دوران جنگ جهانی دوم توسعه یافت و از آن زمان به دلیل خواص متعادل و تولید اقتصادی، به یک جزء اصلی در صنعت لاستیک تبدیل شده است.
وقتی بالغ بر 50 درصد بوتادین و کوپلیمر استایرن را بوتادین تشکیل دهد، آن را SBR می نامند.به طور معمول 70 تا 75 درصد ترکیب مونومرها و یا به عبارتی تکپارها را بوتادین و 25 الی 30 درصد آن را استایرن تشکیل می دهد.
حال به هر دلیلی نسبت استایرن به بیش از 50 درصد برسد، محصول تشکیل یافته شدیدا حالت پلاستیک خواهد داشت که در تهیه و تولید رنگ های شیرابه ای و یا به عبارتی لاتکس به کار می رود. این نوع از پلیمر به صورت پلیمری رایج که دارای کارایی بالایی است، شناخته می شود. به جهت برخورداری از مواد اولیه تولیدی ارزان قیمت این ماده پلیمری که به صورت فراوان هم یافت می شود، آن را تبدیل به پرمصرف ترین و پرکاربردترین لاستیک در سراسر دنیا نموده است. در واقع این ماده پلیمری بالاترین و بیشترین حجم از تولید مربوط به صنعت لاستیک را از آن خود نموده است.
مزایای استفاده از لاستیک SBR
تنوعپذیری: لاستیک SBR میتواند در طیف گستردهای از کاربردها، از خودروسازی تا کالاهای خانگی، استفاده شود و آن را به مادهای متنوع برای تولیدکنندگان تبدیل کند.
عملکرد: خواص مکانیکی عالی آن مانند استحکام کششی بالا و مقاومت در برابر سایش، عملکرد طولانیمدت در محیطهای سخت را تضمین میکند.
مزیت اقتصادی: مقرونبهصرفه بودن لاستیک SBR آن را به گزینهای جذاب برای تولیدکنندگانی که به دنبال تولید محصولات با کیفیت بالا و هزینه کم هستند، تبدیل میکند.
پایداری: به عنوان یک لاستیک مصنوعی، SBR وابستگی به لاستیک طبیعی را کاهش میدهد و به روشهای تولید پایدار کمک میکند.
کاربرد:
صنعت خودروسازی: یکی از کاربردهای اصلی لاستیک SBR در صنعت خودروسازی است. این لاستیک به دلیل دوام و مقاومت در برابر سایش در تولید تایرها، واشرها و مهر و مومها به کار میرود.
تایرها: تایرهای خودرو نیاز به موادی دارند که تحمل سایش بالا، ضربههای مکرر و دماهای مختلف را داشته باشند. SBR به دلیل دوام و انعطافپذیری خود، یکی از مواد اصلی در تولید تایرهای خودرو است.
واشرها اورینگ ها: مقاومت SBR در برابر پارگی و سایش، آن را برای تولید واشرها و مهر و مومهای خودرو که نیاز به دقت و تحمل بالا دارند، ایدهآل میسازد.
صنعت کفش: لاستیک SBR مادهای کلیدی در تولید زیرههای کفش و بوتها است که چسبندگی عالی و طول عمر بالایی دارد.
زیرههای کفش: SBR به دلیل انعطافپذیری و مقاومت در برابر سایش، انتخابی مناسب برای زیرههای کفشهای ورزشی و روزمره است.
بوتها: در تولید بوتها، SBR به دلیل مقاومت در برابر شرایط محیطی سخت و حفظ انعطافپذیری در دماهای پایین، مورد استفاده قرار میگیرد.
صنعت ساختمان: در صنعت ساختمان، SBR برای کفپوش، چسبها و درزگیرها استفاده میشود به دلیل خواص چسبندگی قوی و انعطافپذیری آن (البته ممکن است که به تنهایی استفاده در این محصولات استفاده نشود و با کامپاند کردن ان با سایر لاستیک ها مورد استفاده قرار گیرد.)
کفپوشها: کفپوشهای ساخته شده از SBR به دلیل مقاومت در برابر سایش و قابلیت تحمل بارهای سنگین، در مکانهای پرتردد مانند سالنهای ورزشی و ادارات مورد استفاده قرار میگیرند.
کاربردهای صنعتی: نوارهای نقاله، شیلنگها و سایر محصولات صنعتی از سختی و انعطافپذیری لاستیک SBR بهرهمند میشوند.
نوارهای نقاله: نوارهای نقاله صنعتی نیاز به موادی دارند که تحمل وزن بالا و سایش مداوم را داشته باشند. SBR با خواص مکانیکی برجسته، به عنوان یکی از بهترین گزینهها برای این کاربردها است که البته بسته به کاربرد مورد نظر ممکن است با سایر لاستیک ها به صورت آلیاژ مورد استفاده قرار گیرد.
شیلنگها: شیلنگهای صنعتی ساخته شده از SBR به دلیل مقاومت در برابر فشار و سایش، در صنایع مختلفی مانند نفت و گاز و کشاورزی مورد استفاده قرار میگیرند.
تایر و لاستیک، لوله ها و پوشش های لاستیکی و شیلنگ ها، کابل های سیم کشی، تسمه و نقاله، موکت و کفپوش، زیره و پاشنه کفش و اسفنج و محصولات اسفنجی از دیگر کاربرد های این لاستیک مصنوعی پر مصرف میباشند.یکی از مهم ترین کاربرد های SBR استفاده از آن در ساخت تایر است به خصوص آن قسمتی از تایر که با زمین در تماس است که به آن قسمت تِرِد (Thread) گویند.
5 خاصیت مهم که کاربرد های بالا را برای SBR به ارمغان آورده و آن ر ا برای استفاده عمده در صنعت لاستیک مطلوب کرده عبارتند از:
1- مقاومت پارگی 2- مقاومت خستگی 3- مقاومت فلکس 4- مقاومت سایشی 5- مقاومت در برابر سُرخوردن (خاصیت چنگ زنی به آسفالت را دارد).
کاربردهای نامناسب لاستیک SBR (بهتر است در این موارد با متخصصین مشورت کنید)
در حالی که لاستیک SBR دارای بسیاری از خواص برجسته است، برخی محدودیتها و کاربردهای نامناسب نیز وجود دارد:
محیطهای روغنی و هیدروکربنی: SBR مقاومت کمی در برابر روغنها، گریسها و هیدروکربنها دارد. استفاده از SBR در محیطهایی که با این مواد در تماس هستند میتواند منجر به تخریب و کاهش عمر مفید محصول شود.
دمای بالا: SBR در دماهای بسیار بالا عملکرد مطلوبی ندارد. در کاربردهایی که نیاز به مقاومت در برابر دماهای بالای مستمر دارند، مانند برخی قطعات موتورهای صنعتی، استفاده از SBR مناسب نیست.
اشعه ماوراء بنفش (UV): SBR مقاومت کمی در برابر اشعه UV دارد و در معرض طولانی مدت نور خورشید میتواند دچار تخریب شود. استفاده از SBR در محیطهای باز بدون پوشش محافظ مناسب توصیه نمیشود.
تماس مستقیم با مواد شیمیایی قوی: برخی مواد شیمیایی قوی مانند اسیدهای غلیظ میتوانند به SBR آسیب برسانند. استفاده از SBR در محیطهایی که با این مواد در تماس هستند نیاز به بررسی و آزمایش دقیق دارد.
توجه کنید که این موارد در صورت قرار گرفتن لاستیک در شرایط بسیار سخت و در برار غلظت بالای مواد خورنده برای مدت طولانی پیش میاید که در این صورت نیز راه حل هایی برای این موارد وجود دارد برای مثال میتوان با آلیاژ کردن و آمیخته کردن لاستیک استایرن-بوتادین با سایر لاستیک ها یا اضافه کردن مواد افزودنی به لاستیک این ضفف ها را به شدت کاهش داد و طول عمر لاستیک را تا چند سال اضافه کرد.
فرآیند تولید لاستیک SBR
تولید لاستیک استایرن-بوتادین (SBR) شامل چندین مرحله پیچیده شیمیایی و فیزیکی است که در نهایت منجر به تولید یک ماده با خواص فیزیکی و شیمیایی منحصر به فرد میشود. در این بخش، جزئیات هر مرحله از فرآیند تولید لاستیک SBR را مورد بررسی قرار میدهیم.
انتخاب مواد اولیه
مواد اولیه اصلی برای تولید لاستیک SBR عبارتند از:
استایرن: یک مونومر آروماتیک که به لاستیک SBR خواص مکانیکی خوب و پایداری حرارتی میبخشد.
بوتادین: یک مونومر دیالکین که به لاستیک SBR انعطافپذیری و مقاومت در برابر سایش میبخشد.
پلیمریزاسیون
پلیمریزاسیون فرآیندی است که در آن مونومرها به زنجیرههای پلیمری تبدیل میشوند. دو روش اصلی برای پلیمریزاسیون استایرن و بوتادین وجود دارد:
پلیمریزاسیون امولسیونی:
این روش شامل پلیمریزاسیون مونومرها در یک محیط آبی با استفاده از امولسیفایرها است. این فرآیند در دمای پایین و فشار بالا انجام میشود و به تولید ذرات لاستیک SBR با اندازه یکنواخت کمک میکند. پلیمریزاسیون امولسیونی به دلیل کنترل دقیق روی وزن مولکولی و توزیع اندازه ذرات، بسیار رایج است.
در این روش پلیمریزاسیون از طریق رادیکال های آزاد انجام می شود، که این کار در دو حالت گرم و سرد انجام می شود. محصول بدست آمده از روش سرد در حضور روغن یا در حضور روغن ـ دوده دارای خطیت زیاد، توزیع مولکولی باریک، جرم مولکولی زیاد و فرآیند پذیری دشوار است. (سری 1500 (Type 1500)).
محصول بدست آمده از روش گرم نیز شدیداً شاخه ای بوده و دارای توزیع جرم مولکولی پهن، فرآیند پذیری خوب و درصد 1و2 ـ وینیل بالاتر است. (سری 1000 (Type 1000))
پلیمریزاسیون محلولی:
در این روش، پلیمریزاسیون در یک حلال آلی انجام میشود. این روش منجر به تولید لاستیک با ساختار مولکولی متفاوتی میشود که میتواند برای کاربردهای خاص مورد استفاده قرار گیرد.
در این روش پلیمریزاسیون یونی است، محصول این روش دارای خطیت زیاد، انعطاف بالا و مقاومت سایشی و پارگی بالا در مقابل تنش های دینامیکی است.
روش ژل:
محصول این روش دارای درصد اتصالات شیمیایی ضعیف حین واکنش پلیمریزاسیون بین زنجیره ها است که باعث کم شدن تحرک زنجیره ها و بهبود فرآیند پذیری می شود.
ژل از دو طریق بدست می آید: 1) افزایش دمای پلیمریزاسیون. 2) افزایش موادی مثل دی وینیل بنزن.
فرآوری
پس از پلیمریزاسیون، لاستیک SBR به صورت ذرات کوچک یا محلول در حلالهای آلی تولید میشود. این ماده خام سپس وارد مراحل فرآوری زیر میشود:
انعقاد: در این مرحله، ذرات لاستیک از محلول جدا میشوند. این فرآیند با اضافه کردن عوامل منعقد کننده به محلول لاستیک انجام میشود که باعث جدا شدن لاستیک از حلال میشود.
شستشو: لاستیک منعقد شده به دقت شسته میشود تا هر گونه ناخالصی و مواد شیمیایی باقیمانده از فرآیند پلیمریزاسیون حذف شود.
خشک کردن: لاستیک شسته شده سپس در دستگاههای خشککن خاص خشک میشود تا رطوبت آن کاهش یابد. این مرحله بسیار مهم است زیرا رطوبت باقیمانده میتواند بر کیفیت نهایی محصول تأثیر منفی بگذارد.
افزودنیها
لاستیک SBR خام معمولاً برای بهبود خواص مکانیکی و شیمیایی آن با افزودنیهای مختلفی ترکیب میشود. این افزودنیها شامل موارد زیر میشود:
پرکنندهها: موادی مانند کربن سیاه و سیلیکا که به افزایش استحکام و مقاومت در برابر سایش کمک میکنند.
نرمکنندهها: موادی مانند روغنها که به افزایش انعطافپذیری و پردازشپذیری لاستیک کمک میکنند.
آنتیاکسیدانها: موادی که به جلوگیری از اکسیداسیون و تخریب لاستیک کمک میکنند.
شکنندهها: موادی که به بهبود مقاومت در برابر پارگی و ترکخوردگی کمک میکنند.
فرآوری نهایی
لاستیک SBR با افزودنیهای مختلف مخلوط شده و به شکلهای مختلفی مانند ورقهها، دانهها یا بلوکها فرآوری میشود. این مواد سپس برای استفاده در تولید محصولات نهایی به کارخانههای مختلف ارسال میشود. فرآوری نهایی ممکن است شامل مراحل زیر باشد:
آمیزهکاری: فرآیندی که در آن لاستیک با افزودنیهای دیگر مخلوط میشود تا خواص مطلوبی به دست آید.
پخت: فرآیندی که در آن لاستیک تحت حرارت و فشار قرار میگیرد تا ساختار مولکولی آن تقویت شود و به استحکام و دوام بیشتری دست یابد.
برش و شکلدهی: لاستیک پخته شده به اشکال مختلف برش و شکل داده میشود تا به محصولات نهایی مانند تایرها، واشرها، شیلنگها و غیره تبدیل شود.
نحوه توزیع و چیدمان مونومر ها:
در SBR نحوه چیدمان مونومر ها بسیار مهم است زیرا:
اگر مونومر ها به صورت اتفاقی (Random) کنار هم قرار بگیرند لاستیک استایرن بوتادین (SBR) بدست می آید که خواص و فرآیند پذیری لاستیک ها را دارد.
روش های پخت:
عمدتاً به روش ولکانیزاسیون گوگردی انجام می شود. سرعت پخت در SBR از NR کمتر است بنابراین از شتاب دهنده برای افزایش سرعت پخت استفاده می شود.
کنترل کیفیت
در طول تمامی مراحل تولید، کنترل کیفیت دقیق انجام میشود تا اطمینان حاصل شود که لاستیک SBR تولید شده دارای خواص مطلوب و بدون نقص است. این کنترل شامل آزمایشهای مکانیکی، شیمیایی و فیزیکی بر روی نمونههای تولیدی
____________________________________
بررسی کامل انواع ایزوگام و مشخصات آنها
تا حدود چهل سال گذشته عایقبندی رطوبتی ساختمانها توسط آسفالت و قیرگونی انجام میشد و این روشها معایب زیادی داشت. اما به تدریج با تولید ایزوگام و با توجه به مزایای زیاد این محصولات، عایقبندی ساختمانها در مراحل مختلف از مرحلهی پی و فونداسیون گرفته تا ایزولاسیون دیوارها، عایق کاری سرویسهای بهداشتی و پشت بامها و… توسط این محصولات انجام میشود. ایزوگامها انواع مختلفی دارند که ما در این مقاله شما را با آنها آشنا خواهیم کرد. پس با ما تا انتهای این مطلب همراه باشید.
اساس تقسیمبندی
ایزوگامها انواع مختلفی دارند و برای مصارف مختلفی مورد استفاده قرار میگیرند. انواع ایزوگام بر اساس نوع مواد اصلی تشکیل دهنده، تعداد لایههای تشکیل دهنده، نوع روکش و موارد دیگر تقسیمبندی کرده اند.
با توجه به تولید ایزوگامهای مختلف برای قسمتهای متفاوت ساختمان، برای اجرای انواع ایزوگام، سطح مورد نظر را میبایست به طور دقیق و کامل بررسی کنید و عایق مناسب آن را انتخاب کنید.
انواع ایزوگام براساس ماده تشکیل دهنده
یکی از مهمترین تقسیم بندی های انواع ایزوگام بر اساس مواد اولیه ی تشکیل دهنده ی آنها انجام شده است. بر این اساس، ایزوگام ها به دو نوع تقسیم شده اند که عبارتند از:
۱- ایزوگام پلیمری (BPP) :
ماده اصلی تشکیل دهنده ایزوگام پلیمری، قیر خالص ۷۰-۶۰ است و این قیر از تقطیر نفت خام در پالایشگاه به دست میآید. در اثر حرارت دادن نفت خام در پالایشگاه، بنزین، حلالهای نفتی، نفت چراغ، نفت گاز و دیگر روغنهای سبک آن در برجهای تقطیر جدا شده و در گرمای بیش از حدود ۳۸۰ درجه (در فشار عادی) قیر آن به جا میماند که به صورت جامد یا نیمه جامد است.
علاوه بر قیر خالص ۷۰-۶۰ در تولید این نوع ایزوگام، مواد دیگری شامل: تیشو، پلی استر، پودر تالک ، پلاستیک پشت لایه ایزوگام، فیلم پلی اتیلن، مواد APP درجه ۱ و ۲، لایه آلومینیم ۱۶-۱۴ میکرون، پوشال گونی پلاستیکی در دستگاه ساخت پلیمر مخلوط و پخته میشوند. ترکیب همهی این مواد با هم لایهای محکم ایجاد میکند که از نفوذ هرگونه رطوبت جلوگیری میکند. حاصل پخت این مواد مایع پلیمر است که در اصطلاح عامیانه «شیرهی ایزوگام» نیز گفته میشود. سپس در خط تولید ایزوگام این مایع به لایهی ایزوگام تبدیل میشود.
ایزوگام پلیمری نسبت به ایزوگام دمیده طول عمر و داوم بیشتری دارد و از مقاومت بسیار بیشتری نیز برخوردار است.
انواع ایزوگام براساس لایههای تشکیل دهنده
انواع ایزوگام براساس لایههای تشکیل دهنده
۲- ایزوگام دمیده (BOF):
ماده اصلی تشکیل دهنده ایزوگام دمیده، قیر دمیده شده است که این قیر نسبت به قیر خالص، درجه نفوذ کمتری دارد. علاوه بر این، قیر دمیده که درجه نرمی بیشتری نسبت به قیر خالص دارد، نسبت به تغییرات دما نیز حساسیت کمتری از قیر خالص دارد. قیر دمیده از دمیدن هوا به یک مازوت یا نفت کورهای به دست میآید. به این صورت که هوای داغ با دمای ۲۰۰ تا ۳۰۰ درجه سانتیگراد توسط لولههای سوراخدار به محفظه حاوی مازوت دمیده میشود. در اثر انجام این فرایند، اتمهای هیدروژن موجود در مولکولهای هیدروکربورها، با اکسیژن هوا ترکیب میشود و با تشکیل آب، عمل بسپارش اتفاق میافتد و پس از عمل بسپارش، تبدیل به قیر دمیده میگردد. قیر دمیده تولید شده به افزایش هیچ مادهای نیاز ندارد و به صورت مستقیم وارد دستگاه خط تولید ایزوگام میشود.
علاوه بر قیر دمیده، مواد دیگری شامل: تیشو، پلی استر، الیاف، لایه آلومینیم ۱۶-۱۴ میکرون، پلاستیک پشت لایه ایزوگام، و پودر تالک نیز در تولید ایزوگام دمیده به کار میروند.
این ایزوگام در ساختمانسازی کاربرد چندانی ندارد و در مکانهای با رطوبت کم و تغییر زیاد درجه حرارت به کار میرود. بنابراین بیشتر در باتری اتومبیل، اندودکاری و ساخت ورقهای پوشش بام استفاده میشود. لازم به ذکر است، ایزوگام دمیده نسبت به ایزوگام پلیمری کیفیت کمتری دارد و طول عمر آن نیز کوتاهتر است.
براساس لایههای تشکیل دهنده
یکی از تقسیمبندیهای انواع ایزوگام بر اساس انواع لایههای تشکیل دهنده آنها میباشد. بر این اساس ایزوگامها به سه دسته تقسیم شدهاند که شامل موارد زیر است:
۱- ایزوگام تک لایه :
این نوع ایزوگام تنها از یک لایه پلی استر دوخته شده (سوزنی) ساخته شده است. بنابراین ضخامت کم و انعطافپذیری بالایی دارد و بیشتر برای عایقبندی داخلی استفاده میشود. درواقع این ایزوگامهای تک لایه بیشتر برای عایق کاری مکانهایی که عایق کاری آنها انعطاف بالایی دارد مانند مکانهای قوسی شکل استفاده میشوند.
لازم به ذکر است، ایزوگام تک لایه بیشتر برای عایق کاری مکانهایی که رطوبت کمتری دارند توصیه میشود. یکی از مزایای مهم این ایزوگام قیمت پایین آن است.
۲- ایزوگام دولایه :
این نوع ایزوگام که از دولایه از جنس تیشوی نخ دار (الیاف شیشه) و پلی استر ساخته شده است، با توجه به وجود الیاف شیشه در کنار پلی استر از مقاومت بیشتری نسبت به ایزوگام تک لایه برخوردار است. الیاف شیشه که تیشو نامیده میشوند موجب مقاومت بیشتر ایزوگامها و مانع خم شدن آنها میشوند. همچنین، این نوع ایزوگام جذب قیر بیشتر و استحکام بسیار زیادی دارد. این نوع ایزوگام از طول عمر بالایی نیز برخوردار است و در انواع صنایع مختلف بیشترین کاربرد را دارد.
ایزوگام دولایه بیشتر برای عایق کاری در مناطق مرطوب و سردسیری توصیه میشود.
انواع ایزوگام براساس نوع روکش
یکی دیگر از تقسیمبندیهای ایزوگامها بر اساس نوع روکش پوشش دهندهی آنها میباشد. بر این اساس ایزوگامها به چهار دسته تقسیمبندی شدهاند که به شرح زیر هستند:
۱- ایزوگام با روکش آلومینیومی (فویل دار) :
در تولید این نوع ایزوگام که از یک لایه پلیاستر سوزنی و یک لایه تیشو نخ دار اشباع شده با قیر و اصلاح کنندههای APP تشکیل شده، یک روکش آلومینیومی بر روی سطح عایق کشیده شده است تا مقاومت ایزوگام در برابر نور خورشید افزایش پیدا کند. این روکش بیش از ۸۵٪ گرما را منعکس میکند و از لایهی اصلی ایزوگام در برابر اشعه ماوراء بنفش محافظت میکند.
با توجه به اینکه روکش آلومینیومی میتواند نور را منعکس کند و مقاومت زیادی در برابر نور خورشید دارد این روکش بیشتر در مکانهایی که در معرض تابش نور مستقیم خورشید هستند به کار میرود. درواقع، ایزوگامهای با روکش آلومینیومی بیشتر برای پشت بامها استفاده میشوند.
۲- ایزوگام بدون روکش آلومینیومی (پودری) :
این نوع ایزوگامها همانطور که از اسمشان مشخص است روکش آلومینیومی ندارند و به جای آن از پودر معدنی در تولید آنها استفاده شده است. ایزوگام پودری که از یک لایه پلیاستر سوزنی و لایه تیشو نخ دار اشباع شده با قیر و اصلاح کنندههای APP تشکیل شده، از داخل با نایلکس و از سمت خارج با پودر معدنی پوشیده شده است.
ایزوگامهای پودری یا ساده به دلیل نداشتن روکش مناسب، برای مکانهایی که در معرض تابش نور شدید آفتاب هستند استفاده نمیشوند. ایزوگامهای بدون روکش آلومینیومی بیشتر برای عایق کاری مکانهایی که در معرض نور خورشید نیستند مانند دیوارها، پی ها، سرویسهای بهداشتی، کف استخرها و … استفاده میشوند.
۳- ایزوگام طرح دار :
این نوع ایزوگامها که ایزوگام رنگی نیز نامیده میشوند، با روکشهای طرح دار رنگی یا چاپی پوشانده شده اند. از این نوع ایزوگامهای زیبا که دارای طرحهای آجری، چمنی، شش ضلعی، و همچنین طرح پارکت و سنگ هستند برای عایق کاری نمای بیرونی ساختمان استفاده میشود.
انواع ایزوگام طرح دار
انواع ایزوگام طرح دار
۴- ایزوگام با روکش سنگریزه :
این نوع ایزوگامها با سنگریزههای طبیعی پوشانده شدهاند و با توجه به زیبایی این روکشها بیشتر در مکانهایی که تردد بالایی دارند استفاده میشوند. همچنین، ایزوگام سنگریزهای در عایق کاری نما و پشت بام ساختمان کاربرد دارد و زیبایی خاصی به این مکانها میبخشد.
ایزوگام با روکش سنگریزه
ایزوگام با روکش سنگریزه
بر اساس شکل ظاهری
انواع ایزوگام بر اساس شکل ظاهری و برش روی آنها به دو دسته زیر تقسیم شده اند:
۱- ایزوگام عادی: این نوع ایزوگام همان ایزوگام عادی است که برای همه شناخته شده میباشد و انواع مختلفی دارد و با عرض یک متر و در رولهای ده متری عرضه میشود.
۲- ایزوگام برش خورده (ایزوشینگل): این نوع ایزوگامها برشهای خاص و زیبایی دارند و برای عایق کاری سقفهای شیروانی و نمای ساختمان کاربرد دارند.
انواع ایزوگام بر اساس کیفیت
مهمترین مساله در انتخاب ایزوگام، کیفیت آن و مواد اصلی استفاده شده در تولید آن است. بعضی از مشتریان تصور میکنند هر چه ضخامت ایزوگام بیشتر باشد کیفیت آن نیز بیشتر است. اما این تصور نادرستی است و ضخامت بیشتر ایزوگام به معنی مقاومت بالای آن نیست.
برای انتخاب ایزوگام مرغوب و باکیفیت میبایست به مواد اولیه تشکیل دهندهی آن توجه کنید و دقت داشته باشید که تمامی موارد استاندارد در تولید آن رعایت شده باشد. چون ایزوگام استاندارد مقاومت بسیار زیادی دارد، به راحتی شکسته نمیشود و طول عمر بالاتری نیز دارد.